Hydropower
When renovating an alternator group in a hydro power plant, challenges can pile up rather quickly. Even if works can seem simple compared to other electrical winding jobs, there are many machine-specific issues that require tailored solutions.
Mechanical and physical constraints of the civil infrastructure prohibit major changes to the original design. Aging rotor poles will have sustained mechanical and magnetic stress and slacks on the pole seats and on the rotor are frequent. Interpole connectors often require adjustments to account for this wear. All types of insulation materials are to be expected, including those with asbestos and will need to be addressed promptly.
Wajax | Delstar is aware of all the challenges and peculiarities faced by the hydro power industry. With more than 15 years of experience, we developed innovative solutions so that the choice of your rotor pole manufacturer can be an easy one.
Our services are uniformly available to all types of hydro power plants; tiny, small, medium and large.
Services to the hydropower industry
- Traceable and certified removal, treatment and neutralization of asbestos insulation
- Safe and quick chemical asbestos removal
- Chemical bath capable of 8–24 coils a day
- Rotor pole refurbishment
- Rotor pole manufacturing
- Bonding press capable of 8–24 poles a day
- Manufacturing of dovetail or edge wound coils
- Pole coil refurbishment
- Pole coil manufacturing, dovetail or edge wound
- Automated coil manufacturing machines
- Mini-hydro power plant refurbishment
- Stator connector bars manufacturing
- Electrical tests
- Monitored pressure and temperature, recorded during the hardening process
- Systematic centrifugal and shockwave tests
- Dielectrical tests
- Resistance and impedance tests
- Induced voltage test
- Ohm resistance test
- Hydro power component assembling specialist
- Support toward the development of the manufacturing process to produce stator and rotor electrical components
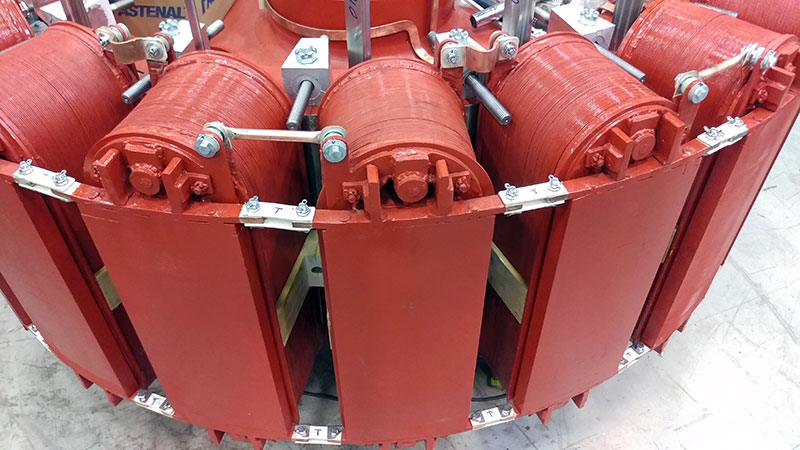